Shaft couplings are essential components in industrial machines that transmit power from one shaft to another. They are mechanical devices that connect two shafts together, allowing them to rotate in unison while compensating for misalignments and other operational issues. Shaft couplings play a critical role in ensuring the smooth operation of industrial equipment and preventing costly breakdowns.
In this article, we will explore the different types of industrial shaft couplings and how to choose the right coupling for your specific needs.
What are Shaft Couplings?
Shaft couplings are mechanical devices that connect two shafts together to transmit power. They come in different types, each with unique characteristics that make them suitable for specific applications. Shaft couplings are designed to compensate for misalignments, reduce vibrations, and prevent the overloading of bearings and other machine components.
Shaft couplings consist of two parts, a driver and a driven element, each connected to one of the two shafts. The driver and driven elements are designed to fit together in a way that allows them to rotate in unison. The connection can be rigid or flexible, depending on the type of coupling.
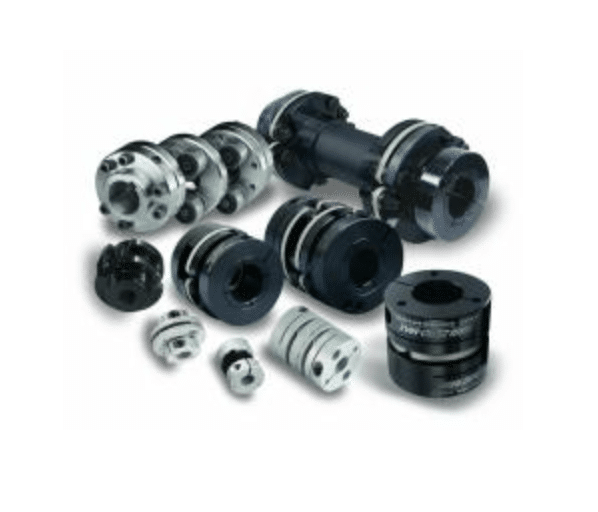
Types of Shaft Couplings
There are two main types of shaft couplings: rigid and flexible. Rigid couplings are designed to transmit torque between two shafts without any misalignment compensation, while flexible couplings are designed to compensate for misalignments and other operational issues.
Rigid Couplings
Rigid couplings are the simplest type of coupling, designed to connect two shafts together without any misalignment compensation. They are typically used in applications where the shafts are perfectly aligned, such as in precision machinery. There are two main types of rigid couplings:
Sleeve Couplings
Sleeve couplings are the simplest type of rigid coupling, consisting of a solid sleeve that fits over the ends of the two shafts. Sleeve couplings consist of a hollow cylinder, or sleeve, that fits over the ends of two shafts and is held in place by setscrews or clamping bolts. Sleeve couplings are easy to install and remove, and they can accommodate a small amount of misalignment between the shafts.
Clamped Couplings
Clamped couplings, also known as split couplings, are designed to clamp onto the shafts using screws or bolts. They are typically used in applications where the shafts need to be connected and disconnected frequently.
Flexible Couplings
Flexible couplings are designed to compensate for misalignments and other operational issues. They are typically used in applications where the shafts are not perfectly aligned, or where there are variations in speed, torque, or vibration. There are several types of flexible couplings:
Elastomeric Couplings
Elastomeric couplings are one of the most common types of flexible couplings. They consist of a flexible elastomeric material, such as rubber, that connects the two shafts. Elastomeric couplings can compensate for both angular and parallel misalignments.
Disc Couplings
Disc couplings consist of a series of thin metal discs that are bolted together to form a flexible connection between the two shafts. They are designed to compensate for angular misalignments and can handle high torque loads.
Gear Couplings
Gear couplings consist of two hubs with external teeth and a flexible sleeve with internal teeth. The hubs are connected to the shafts, and the sleeve connects the two hubs. Gear couplings can handle high torque loads and compensate for angular misalignments.
Grid Couplings
Grid couplings consist of two hubs with a flexible grid coupling element between them. The grid element is designed to absorb shock and vibration and compensate for angular and parallel misalignments.
Jaw Couplings
Jaw couplings consist of two hubs with elastomeric spiders between them. They are designed to compensate for parallel misalignments and handle high torque loads.
Oldham Couplings
Oldham couplings consist of two hubs with a center disc that has slots cut into it. The hubs are connected to the shafts, and the center disc connects the two hubs. Oldham couplings can compensate for angular misalignments and handle moderate torque loads.
Universal Joints
Universal joints consist of two yokes connected by a cross-shaped joint. They are used to transmit torque between two shafts that are not in line with each other. Universal joints can handle angular misalignments and are commonly used in automotive and other mobile applications.
How to Choose the Right Coupling for Your Application
Choosing the right coupling for your application is critical to ensuring optimal performance and reliability. There are several factors that you should consider when selecting a coupling, including torque capacity, misalignment capability, speed and RPM, environment and temperature, and maintenance requirements.
Torque Capacity
The torque capacity of a coupling refers to the maximum amount of torque that the coupling can transmit without slipping or failing. This is an important consideration for applications that require high torque, such as industrial machinery and heavy equipment. When selecting a coupling based on torque capacity, it is important to consider both the maximum torque required by the application, as well as any potential torque spikes or shock loads that may occur.
Misalignment Capability
Misalignment capability refers to the ability of a coupling to compensate for any misalignment between the connected shafts. This is particularly important in applications where the shafts are not perfectly aligned, such as in mobile equipment or in applications where the shafts are subject to thermal expansion. When selecting a coupling based on misalignment capability, it is important to consider both the degree of misalignment that may occur, as well as the type of misalignment (angular, parallel, or both).
Speed and RPM
The speed and RPM of an application can also have an impact on the selection of a coupling. Couplings that are designed for high-speed applications may not be suitable for low-speed applications, and vice versa. When selecting a coupling based on speed and RPM, it is important to consider both the maximum speed and RPM of the application, as well as any potential fluctuations or variations in speed that may occur.
Environment and Temperature
The environment and temperature of an application can also impact the selection of a coupling. Couplings that are exposed to harsh environments, such as those that are subject to dust, moisture, or chemicals, may require special materials or coatings to prevent corrosion and wear. Similarly, applications that are subject to high temperatures may require couplings that are designed to withstand thermal expansion and contraction. When selecting a coupling based on environment and temperature, it is important to consider both the specific conditions of the application, as well as any potential changes or variations in these conditions.
Maintenance Requirements
Finally, the maintenance requirements of couplings can also impact the selection process. Couplings that require frequent maintenance or replacement may not be suitable for applications where downtime is critical, such as in industrial settings. When selecting a coupling based on maintenance requirements, it is important to consider both the frequency and complexity of maintenance tasks, as well as the potential impact of maintenance on overall system performance.
In conclusion, shaft couplings play a critical role in ensuring the smooth operation of industrial machinery and preventing costly breakdowns. Understanding the different types of shaft couplings and their unique characteristics is essential to choosing the right coupling for your specific application.
Feel free to visit HVH Industrial Solutions if you have any questions, need more information, or are interested in purchasing a shaft coupling.
Also, you can check our Engineering Blog for more informative articles.
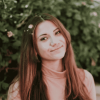
Angela Spearman is a journalist at EzineMark who enjoys writing about the latest trending technology and business news.