In the ever-evolving world of manufacturing, ensuring product quality and reliability is more critical than ever. As industries push the boundaries of materials and designs, traditional quality control methods are being replaced by advanced techniques such as Ultrasonic Testing (UT). But how exactly is ultrasonic testing revolutionising modern manufacturing quality control, and why is it becoming the go-to method for detecting defects and ensuring structural integrity?
Understanding Ultrasonic Testing
Ultrasonic Testing is a non-destructive testing (NDT) method that uses high-frequency sound waves to detect internal and surface flaws in materials. It works by transmitting ultrasonic waves into the material and analyzing the reflected signals to identify inconsistencies such as cracks, voids, and inclusions. This method offers unparalleled accuracy, making it an invaluable tool for industries where safety and performance are paramount.
The principle behind UT is straightforward: sound waves travel through a medium and reflect when they encounter a boundary or defect. The time taken for the echoes to return is analyzed to determine the location and size of the flaw. This process enables manufacturers to inspect components without causing damage, thereby ensuring product reliability and longevity.
Key Benefits of Ultrasonic Testing in Manufacturing
The growing adoption of ultrasonic testing in modern manufacturing is largely due to its numerous benefits over traditional inspection methods. Some of the key advantages include:
- High Precision and Accuracy
UT can detect minute defects that are often missed by other NDT methods, making it a preferred choice for critical applications such as aerospace, automotive, and energy sectors. - Non-Destructive Nature
Unlike destructive testing methods, UT allows manufacturers to inspect materials without compromising their usability. This is particularly crucial for expensive or critical components. - Speed and Efficiency
Ultrasonic inspections are quick and can be performed in real-time, enabling manufacturers to maintain production schedules without significant downtime. - Cost-Effectiveness
Early defect detection through UT helps prevent costly rework and potential failures, reducing overall operational costs and enhancing productivity. - Versatility
UT can be applied to a wide range of materials, including metals, composites, and plastics, making it suitable for diverse manufacturing industries.
Applications of Ultrasonic Testing in Modern Industries
Ultrasonic Testing has become an indispensable quality control tool across various manufacturing sectors. Some of the most prominent applications include:
● Aerospace Industry: Ensuring the structural integrity of aircraft components, including wings, fuselage, and turbine blades.
● Automotive Manufacturing: Inspecting engine parts, welds, and critical safety components such as suspension systems.
● Oil and Gas Industry: Evaluating pipeline integrity to prevent leaks and potential environmental hazards.
● Power Generation: Assessing turbine blades, pressure vessels, and heat exchangers for potential failures.
● Medical Equipment Manufacturing: Verifying the integrity of implants and prosthetics to meet stringent safety standards.
Advanced Developments in Ultrasonic Testing
With the advent of digital technologies, ultrasonic testing has evolved significantly, offering enhanced capabilities and automation. Some of the latest advancements include:
● Phased Array Ultrasonic Testing (PAUT): This technique uses multiple elements to steer and focus sound waves, allowing for a more detailed and comprehensive inspection of complex geometries.
● Automated Ultrasonic Testing (AUT): Robotic and automated scanning solutions have improved efficiency and repeatability in high-volume manufacturing environments.
● Data Analytics and AI Integration: Machine learning algorithms are being used to analyze UT data, providing predictive maintenance insights and reducing human error.
Challenges and Considerations
Despite its many advantages, ultrasonic testing does come with certain challenges that manufacturers must consider:
● Operator Expertise: Proper training and certification are required to ensure accurate interpretation of results.
● Surface Preparation: Rough or uneven surfaces may impact the accuracy of readings, requiring careful preparation.
● Material Limitations: Some materials, such as porous or highly attenuative materials, may pose challenges for effective UT inspection.
Conclusion
Ultrasonic Testing is revolutionising modern manufacturing quality control by providing accurate, efficient, and non-invasive inspection capabilities. As industries continue to prioritize safety and performance, UT’s role will only grow, driven by technological advancements and increasing demand for high-quality products.
By integrating ultrasonic testing into their quality assurance programs, manufacturers can achieve higher reliability, reduce costs, and gain a competitive edge in the market. The future of manufacturing lies in smarter, more precise inspection methods—are you ready to embrace the revolution?
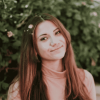
Angela Spearman is a journalist at EzineMark who enjoys writing about the latest trending technology and business news.